Things about Lean Manufacturing
Table of ContentsWhat Does Oem Mean?Fascination About Lean ProductionThe Single Strategy To Use For Additive ManufacturingFacts About Mfg RevealedExcitement About MfgThe Only Guide for Lean Production
The message on this web page is an example from our complete White Paper 'Shot Moulding for Buyers' - * Example message * - for full guide click the download button above! Intro This overview is planned for individuals that are aiming to source plastic mouldings. It provides a much needed understanding into all that is involved with developing plastic parts, from the mould tool called for to the moulding procedure itself.If you desire to explore even more, the guide covers types of mould tools, in addition to special ending up processes such as colours & plating. Words that are underlined can be discovered in the reference in the appendix ... Part I: Moulding: The Fundamentals The Advantages of Shot Moulding Plastic injection moulding is a very accurate process that offers several advantages over other plastic processing methods.
Precision is excellent for extremely detailed components. You can hold this moulding in the hand of your hand and it has bosses, ribs, metal inserts, side cores and also openings, made with a moving shut off feature in the mould tool.
The Facts About Die Casting Uncovered

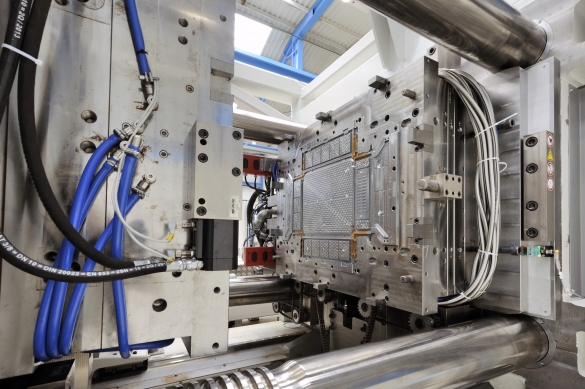
from material feed Product melting; material injection; shot time cooling down ejection as well as the re-closing of the mould tool ready for all set next cycleFollowing Draft angles - The wall surfaces of a moulded component should be a little tapered in the direction in which the component is ejected from the mould device, to permit the part to be ejected easily.
Ejector stroke - The pressing out of ejector pins to expel the moulded part from the mould tool. Ejector stroke rate, length and timing needs to be thoroughly regulated to avoid damages to the ejectors and mould tool, yet at the exact same time make the moulding cycle as short as possible.
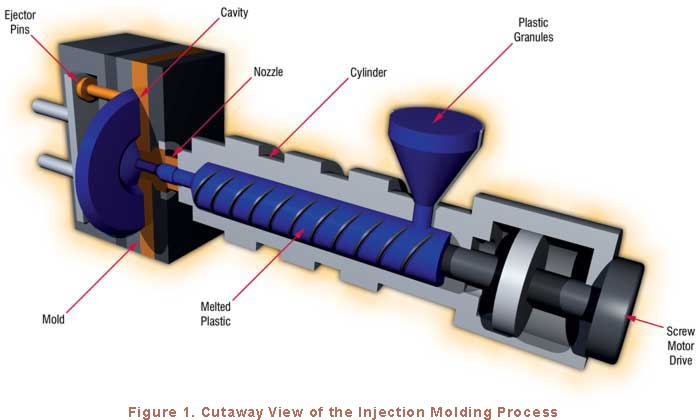
Plastic Manufacturing Things To Know Before You Buy
Ribs steel manufacturing - When a plastic component has slim walls, ribs are contributed to the style to make the thin walls more powerful Side cores - Side action which generates an attribute on a moulded part, at an opposing angle to the typical opening instructions of the mould tool. manufacturing. The side core requires to be able to withdraw as the plastic component can not be ejected otherwise.
Wall surfaces - The sides of a moulded component The message on this web page is a sample from our full White Paper 'Shot Moulding for Purchasers'.
Manufacturing procedure for producing components by injecting molten material right into a mould, or mold and mildew Simplified layout of the process Shot moulding (U.S. punctuation: injection molding) is a manufacturing process for producing parts by infusing molten product into a mould, or mold. Injection moulding can be carried out with a host of products mostly including steels (for which the process is called die-casting), glasses, elastomers, confections, and most commonly polycarbonate as well as thermosetting polymers. Injection moulding is commonly utilized for manufacturing a variety of parts, from the tiniest elements to whole body panels of vehicles. Injection moulding uses a special-purpose check my site maker that has 3 components: the shot unit, the mould and the clamp.
Rumored Buzz on Manufacturing
, with the volume utilized of the former being significantly higher.: 13 Thermoplastics are prevalent due to attributes that make them extremely suitable for shot moulding, such as ease of recycling, flexibility for a vast selection of applications,: 89 as well as capacity to soften and flow on home heating.
In several cavity moulds, each cavity can be the same and develop the very same components or can be unique and create several different geometries during a single cycle.
When sufficient product has actually gathered, the material is forced at high stress and speed right into the component forming tooth cavity. The precise quantity of shrinking is a feature of the material being made use of, and can be reasonably foreseeable. To stop spikes in stress, the process usually uses a transfer placement representing a my site 9598% full tooth cavity where the screw changes from a constant speed to a continuous pressure control.
The Only Guide to Oem
The packaging pressure is used until the gateway (cavity entryway) solidifies. Due to its small dimension, the gateway is usually the very first location to solidify with its whole thickness.: 16 Once the entrance solidifies, no more product can get in the cavity; as necessary, the screw reciprocates and also acquires product for the next cycle while the product within the mould cools so that it can be ejected and be dimensionally stable.